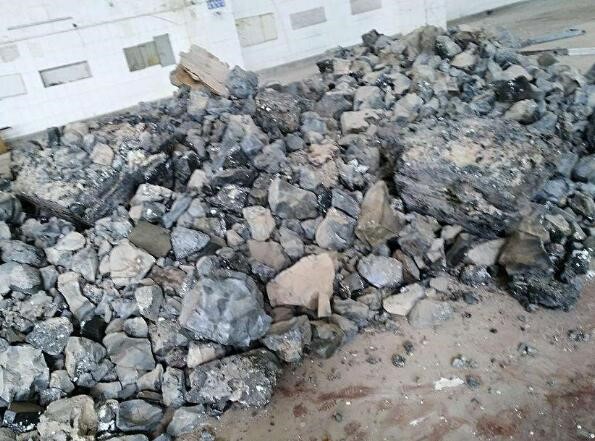
对于 Pt、Pd、Rh 含量 1000~2000g/ t 的汽车废催化剂,我国采用加压氰化法提取其中的 Pt、Pd、Rh,废催化剂预处理脱除载体中的油污、积碳,通过 2 次加压氰化浸出,Pt、Pd、Rh 的回收率分别达到 95%~96%、97%~98%、90%~92%。虽然,工艺中使用的氰化物有毒,但在高温高压下溶液中的氰化物被转化为的碳酸盐,残余氰化物浓度很底,排放无害。
美国针对含(g/t) :Pt 1220,Pd 170,Rh140 的废催化剂,以金属铁粉为捕集剂,少量碳作还原剂,加石灰熔剂进行等离子熔炼(破碎后的粉状废催化剂:石灰:铁:碳~100:10:1~3:1)。熔炼温度约 1500℃,所有粉状物料混合后喷射入炉,传热、传质快。载体与熔剂化合转变为炉渣,获得带磁性的含铂族金属约 7%的铁合金,可以磁选回收。铁合金相的产率,即铂族金属在铁合金中的富集倍数,取决于铁粉加入量,报道的熔炼回收率(%) :Pt>99,Pd >98,Rh约 87。
氧化铝废钯(铂)废催化剂、汽车钯炭催化剂及其它废催化剂共有2种工艺路线。个过程是:载体的选择性溶解、难溶渣、贵金属的溶解、分离和提纯。二是溶解贵金属,分离提纯。
钯(铂)碳废催化剂和废电子浆料等废料的工艺路线是焙烧、焙烧渣、溶解贵金属及分离提纯。
废钯(铂)电镀液的工艺路线为置换、置换渣、溶解贵金属、分离提纯。
对于钯(铂)废电子元件(集成电路板、触点、触点),将工艺路线分为分解、焙烧、焙烧渣、贵金属溶解、分离提纯等。
需要指出的是,无论采用何种技术,都必须有完善的环保设施。例如,焙烧炉应配备完善的除尘设备,废气和废水达标排放。